Austenitic steel represents one of the most important and widely used categories in the field of stainless steels. This class of steels is characterized by the presence of an austenitic crystalline structure that is stable at room temperature due to a specific chemical composition that includes high percentages of chromium and nickel.
Table of Contents
Toggle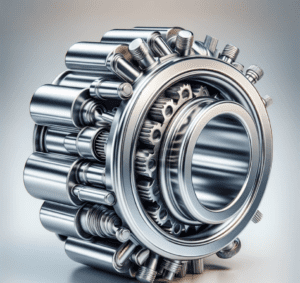
Chemical Composition and Structure
Austenitic steels generally contain between 16 percent and 25 percent chromium and between 8 percent and 20 percent nickel. The combination of these elements gives them an austenitic microstructure, which is a face-centered cubic (FCC) crystal structure. This type of structure is stable at all temperatures, unlike other crystal structures such as ferrite or martensite that can transform at different temperatures.
Main Properties
Corrosion Resistance
One of the main advantages of austenitic stainless steels is their excellent corrosion resistance. Chromium forms a passivating layer of chromium oxide on the surface of the steel, protecting it from corrosion. The presence of nickel further enhances this property, making austenitic stainless steels ideal for aggressive environments.
Ductility and Formability
Austenitic stainless steels are known for their excellent ductility and formability. They can be easily machined, bent and welded without losing their mechanical properties. This makes them suitable for a wide range of applications, from the food industry to chemical plant construction.
Tenacity at Low Temperature
Another distinguishing feature of austenitic steels is their toughness at low temperatures. Unlike other categories of steels, they retain their strength and ductility even at very low temperatures, making them suitable for cryogenic applications.
Classification of Austenitic Steels
Austenitic steels are divided into several subcategories, including:
- 300 Series: The most common series of austenitic stainless steels, which includes the famous AISI 304 and AISI 316. 304 is the most widely used austenitic stainless steel due to its balance of cost and performance, while 316 offers greater corrosion resistance due to the addition of molybdenum.
- 200 Series: These steels contain less nickel and more manganese. They are used in less critical applications where cost is a determining factor.
Chemical Nickel Plating: An Innovative Surface Treatment
Chemical nickel plating, also known as autocatalytic nickel plating, is a process of chemical deposition of nickel on a metal surface without the use of electricity. This process occurs through a chemical reaction in a solution containing nickel ions, which reduces the nickel on the surface of the metal, creating a uniform, dense coating.
Benefits of Chemical Nickel Plating on Austenitic Steels
The application of chemical nickel plating on austenitic stainless steels offers numerous advantages, further improving the already excellent properties of these materials. Let’s see how chemical nickel plating can benefit each of the applications of austenitic stainless steels:
Food Industry
Chemical nickel plating on austenitic stainless steels used in the food industry can significantly improve corrosion resistance, especially in acidic or alkaline environments. This treatment creates a smooth and uniform surface that prevents the adhesion of bacteria and facilitates cleaning, ensuring improved hygiene and food safety.
Construction and Architecture
In the construction and architectural sectors, chemical nickel plating can protect austenitic stainless steel structures from weathering and wear. This treatment increases the durability of facades, railings, and other exposed structures, reducing maintenance costs and extending the life of installations.
Chemical and Petrochemical Industry
Austenitic stainless steels used in chemical and petrochemical plants can benefit greatly from chemical nickel plating. This coating provides additional protection against corrosion from aggressive chemicals, improving the strength and reliability of reactors, tanks, and piping.
Marine Applications
In marine environments, chemical nickel plating on austenitic steels provides excellent protection against corrosion caused by salt water. This treatment is particularly useful for ship components, offshore platforms, and other marine structures, where corrosion resistance is crucial for safety and durability.
Medicine and Biotechnology
In medical and biotechnology, chemical nickel plating can improve the properties of surgical instruments and medical devices made of austenitic stainless steel. This treatment creates a harder and more wear-resistant surface, increasing the life of the instruments. In addition, chemical nickel plating can improve the biocompatibility of surfaces, reducing the risk of adverse reactions in patients.
Due to its excellent properties of corrosion resistance, ductility, formability and low temperature toughness, austenitic steel is a key material in many industrial and commercial applications. The integration of chemical nickel plating as a surface treatment can further
mind improving the performance of austenitic stainless steels, offering additional advantages in corrosion resistance, hardness, surface uniformity, and ease of maintenance.
Insight into Chemical Nickel Plating
Chemical nickel plating does not require the use of electric current, unlike electroplating, and is based on an autocatalytic process. The nickel solution, containing a reducing agent such as sodium hypophosphite, allows uniform deposition of nickel on complex and irregular surfaces. This makes chemical nickel plating particularly suitable for components with complex geometries or difficult to coat by other methods.
Specific Advantages of Chemical Nickel Plating on Austenitic Steels
- Uniformity of Coating: Chemical nickel plating provides uniform coverage even on intricate surfaces, corners, and recesses, improving the overall performance of austenitic stainless steel components.
- Increased Hardness: Electroless nickel coating can increase the surface hardness of austenitic steels, improving abrasion and wear resistance. This is especially useful in mechanical applications and in environments with abrasive particles.
- Friction Reduction: The smooth and uniform surface achieved by chemical nickel plating reduces friction between components, improving operational efficiency and reducing wear. This benefit is crucial in applications such as gears, bearings and valves.
- Antimicrobial Properties: The nickel-plated surface may have antimicrobial properties, reducing bacterial growth. This is especially advantageous for applications in the food and medical industries, where hygiene is critical.
Specific Applications Enhanced by Chemical Nickel Plating
Food Industry
Chemical nickel plating improves the corrosion resistance of austenitic stainless steels, preventing contamination of food products. It also facilitates cleaning and maintenance of equipment, ensuring high hygienic standards.
Construction and Architecture
Architectural structures made of austenitic stainless steel, once chemically nickel-plated, show enhanced resistance to weathering and vandalism. The protective coating reduces the need for frequent and prolonged maintenance, preserving aesthetics and functionality over time.
Chemical and Petrochemical Industry
The protection offered by chemical nickel plating against aggressive chemicals is essential for the longevity of austenitic stainless steel components. This treatment increases corrosion resistance in extremely corrosive environments, improving the reliability and safety of installations.
Marine Applications
Austenitic steels used in marine environments benefit from chemical nickel plating through enhanced corrosion resistance from salt water and salt spray. This treatment is critical for critical components such as ship hulls, offshore platform equipment, and underwater instruments.
Medicine and Biotechnology
Surgical instruments and medical devices made of chemically nickel-plated austenitic stainless steel are more resistant to wear and corrosion. The hard, smooth surface improves sterilization and reduces the risk of nosocomial infection, increasing patient safety.
Austenitic steel, already renowned for its corrosion resistance, ductility and toughness, finds chemical nickel plating a valuable ally to further improve its properties. This surface treatment offers additional protection, increasing the durability and performance of components in a wide range of applications. The combination of austenitic stainless steels and chemical nickel plating is an ideal match to meet the needs of diverse sectors, from the food industry to the medical industry, from construction to the chemical industry, confirming the central role of these materials in innovation and technological development.
EXAMPLES OF APPLICATION in different fields:
Chemically nickel-plated austenitic steel is widely used in multiple industries because of the many advantages of this surface treatment. Here are some examples of specific components that benefit from chemical nickel plating:
Examples in the Food and Beverage Sector
- Storage Tanks: Austenitic steel tanks used for food and beverage storage can be chemically nickel-plated to improve corrosion resistance and facilitate cleaning. This treatment prevents contamination and ensures food safety.
- Conveyor Belts: Austenitic stainless steel conveyor belts, often used in food processing plants, are chemically nickel-plated to reduce friction and prevent wear and tear, extending operating life and reducing maintenance downtime.
Examples also in the Chemical and Petrochemical Sectors.
- Chemical Reactors: Austenitic steel chemical reactors, which are exposed to aggressive chemicals, are often chemically nickel-plated to increase corrosion resistance and improve long-term structural integrity.
- Heat Exchangers: Heat exchangers made of austenitic stainless steel can be chemically nickel-plated to prevent corrosion from process fluids, improving thermal efficiency and durability.
Applications in the Marine and Offshore Sectors
- Vessel Components: Vessel parts such as valves, pumps, and fittings made of austenitic steel are chemically nickel-plated to withstand the highly corrosive marine environment, ensuring greater durability and reliability.
- Offshore Structures: Offshore oil platforms use chemically nickel-plated austenitic stainless steel components to resist corrosion caused by salt water and extreme weathering.
Employment in the Medical and Biotechnology Sector.
- Surgical Instruments: Surgical instruments made of austenitic steel, such as scalpels and forceps, are chemically nickel-plated to improve corrosion resistance, hygiene, and durability, reducing the risk of infection during operations.
- Medical Devices: Components of implantable medical devices, such as stents and prostheses, are often chemically nickel-plated to increase biocompatibility and prevent internal corrosion in the human body.
Uses in the Automotive and Aerospace Sectors.
- Engine Components: Parts of austenitic steel engines, such as shafts and bearings, are chemically nickel-plated to increase wear resistance and improve long-term performance.
- Aerospace Components: Critical austenitic stainless steel components used in aerospace applications, such as joints and fittings, are chemically nickel-plated to ensure corrosion resistance and reliability under extreme conditions.
Use in the Electronic Industry
- Electrical Connectors: Austenitic steel connectors used in electronic devices are chemically nickel-plated to improve electrical conductivity and prevent corrosion, ensuring safe and durable connections.
- Printed Circuit Board Components: Some austenitic stainless steel printed circuit board components can be chemically nickel-plated to increase wear resistance and improve durability.
Construction Sector
Architectural Facades
Austenitic steel building facades, which must maintain an impeccable aesthetic appearance and resist weathering, are often chemically nickel-plated to provide long-term protection.
use on Railings and Balconies
Austenitic stainless steel railings and balconies, exposed to variable weather conditions, benefit from chemical nickel plating to prevent corrosion and maintain structural integrity.
F.A.Q.
Here are some of the most frequently asked questions on the Internet about austenitic steels, along with brief answers and explanations:
- What is austenitic steel?
Austenitic steel is a category of stainless steels characterized by an austenitic crystalline structure, achieved by a high chromium and nickel content. This microstructure gives the steel remarkable corrosion resistance, excellent ductility and toughness even at low temperatures(SASSDA)(Joining Innovation with Expertise).
- What are the most common types of austenitic steels?
The most common types of austenitic steels belong to the 300 series, particularly stainless steel 304 and stainless steel 316. Steel 304 is known for its good corrosion resistance and versatility, while steel 316, containing molybdenum, offers superior corrosion resistance in marine or chemical environments (SASSDA)(Joining Innovation with Expertise).
- Are austenitic steels magnetic?
In general, austenitic steels are not magnetic because of their austenitic structure. However, under certain processing conditions, such as welding or plastic deformation, they may exhibit some magnetic properties due to the formation of martensite(SS303)(SASSDA).
- What is the difference between austenitic stainless steel and other types of stainless steels?
Stainless steels can be divided into several categories, including ferritic, martensitic, duplex, and austenitic; austenitic steels are known for their corrosion resistance and ductility, while ferritic and martensitic steels offer higher hardness and mechanical strength but lower corrosion resistance. Duplex steels combine properties of austenitics and ferritics, offering a good balance of mechanical and corrosion resistance(Boyd Metals – Blog)(SASSDA).
- Can austenitic steels be welded?
Yes, austenitic steels can be successfully welded. It is important to use the correct electrode or stainless steel welding wire to avoid intergranular corrosion problems and ensure the quality of the welded joint. Also, during welding, it is critical to control the formation of chromium carbides, which can reduce corrosion resistance (Boyd Metals – Blog)(Joining Innovation with Expertise).
- How do you heat treat austenitic steels?
Austenitic steels cannot be hardened by traditional heat treatment like carbon steels. However, they can be annealed to relieve internal tension and improve pliability. Solution treatment, which involves heating to high temperatures followed by rapid cooling, is commonly used to restore the austenitic microstructure(SS303)(Joining Innovation with Expertise).
- What are the common applications of austenitic steels?
Austenitic steels find applications in numerous fields, including:
- Food industry: for manufacturing equipment and containers due to their corrosion resistance and ease of cleaning.
- Construction: in architectural facades and structures exposed to weathering.
- Chemical and petrochemical industry: for reactors, piping and tanks resistant to aggressive chemicals.
- Marine applications: for ship components and offshore platforms.
- Medicine and biotechnology: for surgical instruments and medical devices due to their biocompatibility and corrosion resistance(SASSDA)(Joining Innovation with Expertise).
These questions cover some of the main aspects of austenitic steels and their applications, reflecting the interest and relevance of this material in various industrial and technological fields.